We have developed advanced energy management systems based on IIOT which enables you to monitor the energy consumption in your industrial facility and thereby increase the efficiency of your system. By the utilization of most modern IOT facilities, you can leverage the advantages of cloud systems, which in turn helps in data logging, reporting and provide historical trends for the electrical power consumption in your industrial facility.
IIOT-Industrial Internet of Things
Industrial Internet of Things (IIoT) refers to the use of IoT concepts in industrial production. In the German-speaking world, the Industrial Internet of Things is often referred to as Industry 4.0. Compared to the Internet of Things in the private sphere (IoT), the focus in the industrial sector is on the networking of machines (machine-to-machine) and seamless process chains. The key concept of the IIoT is thus to integrate machine learning and big data technologies and thus considerably increase the effectiveness of companies. However, complexity and requirements are much higher in IIoT than in IoT.
What's the Importance of Industry 4.0?
The Fourth Industrial Revolution, or Industry 4.0, is extremely relevant and increasingly important in manufacturing for a multitude of reasons. Put as simply as possible, Industry 4.0 represents the next wave of technology driving efficiency across operations.
Failing to adopt technology of the Fourth Industrial Revolution will cause organizations to fall behind, as their operations will not be digitized enough to match competitors.
Why is Industry 4.0 Important in Manufacturing?
There are several key reasons why Industry 4.0 technologies will increasingly be adopted by manufacturers:
Cost Efficiency: Machine Monitoring solutions, predictive maintenance strategies, and other advanced operational technology will help manufacturers decrease downtime, increase throughput, and overall, reduce the cost of supplying quality parts.
Democratizing Data: Along with many other industries, manufacturing has suffered from siloed data, not only among separate departments within the organization, but also at different levels (ie. the machine level, the plant level, corporate). A connected operation provides accessibility to disparate data sources, and if done properly, provides an easy way to use that data for effective decision-making.
Operational Agility: Being able to quickly react to fluctuating demand, new product trends, the skills gap, and other unpredictable challenges is key for any manufacturer. With the right technology in place, manufacturers have a greater likelihood to successfully pivot when experiencing adversity.
Documentation and Traceability: With digitized information, a nearly limitless amount of manufacturing data can be stored via the cloud. What this means is that all manually collected information can be converted to a digitized data collection system, which can be used for anything from training new workers with legacy knowledge, to building advanced algorithms with historical data. The options are unlimited as long as the data is stored and accessible in such a way to build solutions.
Retaining Customers: Power among suppliers and consumers has continued to trend towards the customer, with increasing expectations around service and product quality. To meet these rising demands, manufacturers will be forced to adopt technology to support customization, product development, after-sale service, and more.
Our Commitment.
Team Hedge Will support you to think about where your organization is now and where you plan to be in the future and We together will Implement It.
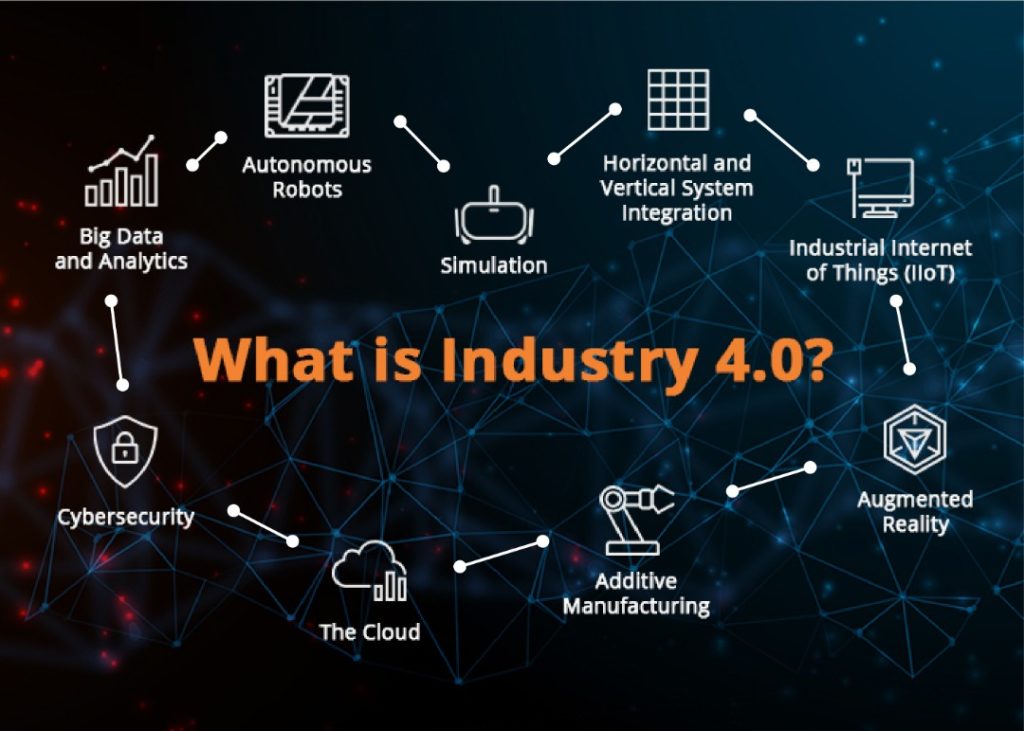